
The booklet was partly educational and partly a sales brochure to make you want to buy more cutters. Several examples of cut profiles were made with a combination of cuts from two or more cutters set very orecisely. Whenever you bought a sawblade at Sears you got a small booklet with a complete list and drawings to show the profile of all cutters offered by Craftsman. And, guards sometimes got in the way more than they protected. Although you could buy a guard, great care was needed to be certain fingers did not get into the path of the virtually invisible spinning blades. Any warp or twist in the wood meant an uneven cut was likely. That is because the cutter is likely above on the radial arm saw and the work can jump up into the cutters if not held down very well. Chatter was more of a problem on a radial arm saw than I think it would be on a table saw. Chatter was also something to be avoided, if at all possible. I had to be very careful to feed work slowly at an even speed or there could be a scallop from uneven cutting. A router seemed like a luxury item not affordable. The peripheral speed was pretty good, but they still did not cut quite as well as a router. These cutters naturally were not carbide tipped, but ground. I made a plywood table to fit on the lathe so I could use the cutters to make molding. Before the radial arm saw I had a solid blade mount arbor for a wood lathe I had bought a dozen years before while in junior high. Antiquing was popular then, so I could use soft woods because the antiquing meant they got a coat of paint and the grain pattern did not matter. I got a radial arm saw in 1972 and used these to make Roman Ogee molding for tops on our first bedroom furniture pieces.

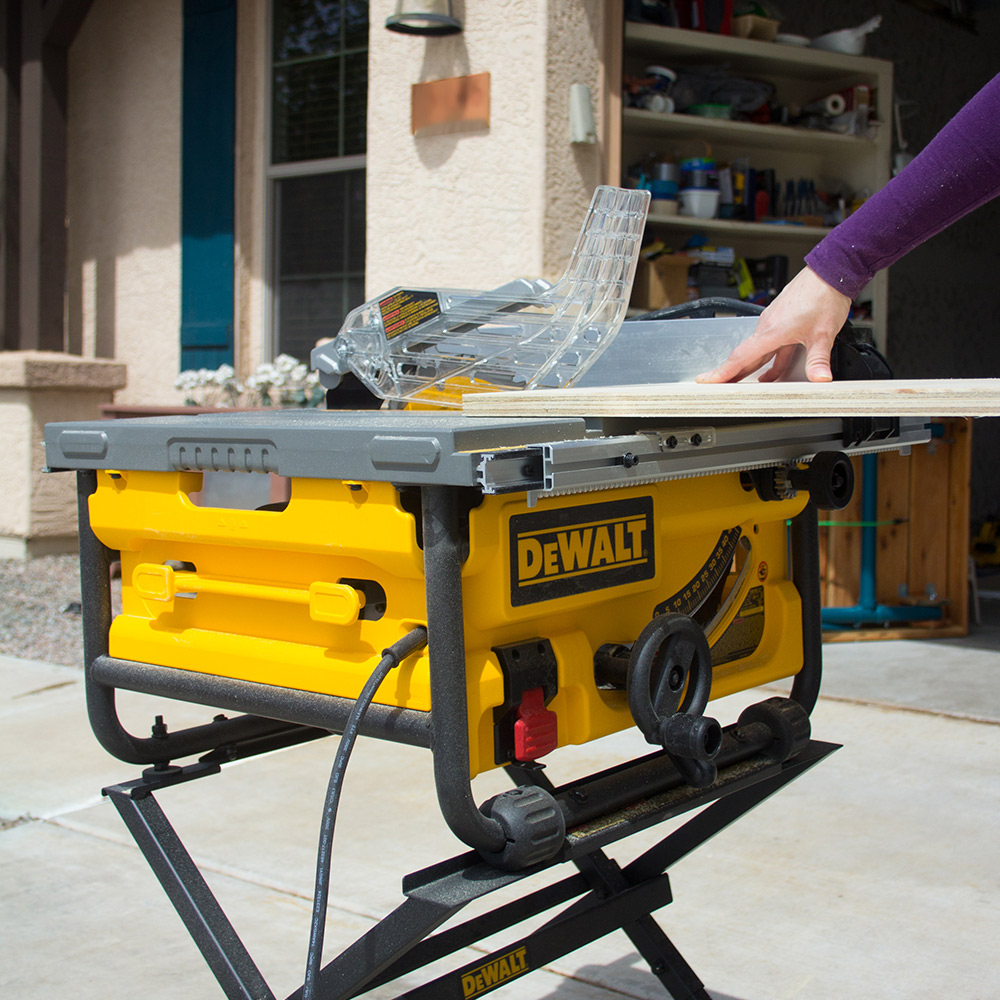
I coveted a cutter head and a few basic cutters back in the early 1970s. I took off so little material that this happened in one pass as well. I then changed the blade to a cove profile and for each outer edge. Hear I set the depth to just make the flutes on one pass and barely take away any wood at the highest height of the flute so I didn't have to make multiple passes. If you run one piece, then adjust and run another you may not make the depth or position correctly and have molding that doesn't match up. For example, if you have to make multiple passes at different depths, then run all of the wood through at each adjustment so that it remains uniform.
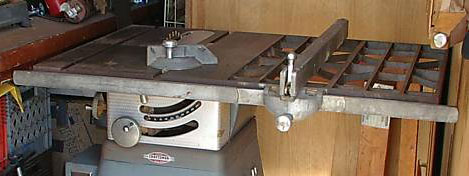
If you've got multiple pieces of molding to make you'll want to run all of it through the setup before making any changes. Use a test strip to get your depth set right or to figure out if you need to make the cut over several passes at gradually increasing depth. You don't want to take too much as this will slow down the speed you can put the wood through. My saws dado insert would have worked fine, but I wanted a little extra support after the wood came out of the blade.Īdjust the depth of the blade to take off just the right amount of wood. The only thing to be careful of is where you put your screws in this thing. 1" wide fence add-ons make it easier to do the math when you still want to use the fence's measuring tape. You could easily make one for each of the different profiles if you wish, but I just made this one with the 1" straight edged joiner profile blade so that any of the blades would work with it. My old saw's design makes it a little tricky to make a wooden zero clearance insert so I made one that sits on top of the table and is part of the fence. You could seriously damage your fence and have flying shards of profile blades going everywhere if you ran your metal fence into while running. Some profile blades you could probably get away without it, but I wouldn't. I don't think this is really optional if you want to use this safely.
